What if you could prevent equipment breakdowns and save time, labor, and money? Then, preventive maintenance in manufacturing is the answer. The benefits of IoT preventive maintenance solutions are, on average: a 25% increase in productivity, a 70% breakdown reduction, and a 25% decrease in maintenance costs.
What Is Preventive Maintenance in Manufacturing?
In a smart factory, IoT-enabled sensors monitor and collect data from machines in real-time. Then, a preventive maintenance system evaluates the conditions of the equipment based on that data and detects anomalies. This allows engineers to schedule downtime precisely to replace parts or perform other maintenance tasks without causing costly disruptions to the production process.
Preventive Maintenance Versus Reactive Maintenance
Reactive maintenance is the traditional form of maintenance, meaning acting once a failure has occurred. It may disrupt the manufacturing processes, causing unplanned, and expensive, downtime.
On the other hand, preventive maintenance means acting before a failure occurs, enabling immediate action. This proactive approach results in reduced downtime and costs, along with increased productivity.
Benefits of Preventive Maintenance in Manufacturing
Preventive maintenance has many benefits, especially in the manufacturing sector:
- Better ROI: Predictive maintenance reduces unplanned downtime and eliminates unnecessary tasks, resulting in cost savings.
- Longer machinery lifespan: The system alerts about problems well before they cause serious damage.
- Less waste: It allows engineers to fix sub-optimal operations before machines start producing defective products, reducing waste materials in the process.
- Improved performance: It reduces the time and frequency of repairs.
- Equipment protection: It prevents damage to other parts of the machine while repairing it.
Using OEE Formulas for Manufacturing Efficiency
One of the key factors in achieving manufacturing efficiency is understanding and utilizing OEE (Overall Equipment Effectiveness) formulas. OEE is a measure of how well manufacturing equipment is performing, and it considers factors like availability, performance, and quality. Here’s a breakdown of the components:
Availability: OEE availability measures the actual run time of a machine compared to the planned run time. It helps identify instances of planned stops and unplanned downtime.
Performance: This aspect of OEE looks at the machine’s speed compared to its ideal cycle time. It helps in identifying issues like slow cycles and small stops that affect efficiency.
Quality: OEE quality standards measure the ratio of good parts produced to the total parts produced. It focuses on eliminating waste due to defects.
By applying OEE formulas and principles, including preventive maintenance, manufacturers can gain insights into their operations, pinpoint areas for improvement, and enhance overall efficiency.
Implementing OEE with 4i Platform
The 4i Platform team has developed a web-based app, ELT, that empowers manufacturers to implement OEE and achieve significant improvements. Our ELT app monitors your assets in real-time to detect potential breakdowns and improve efficiency.
Implementing ELT leads to several benefits:
- 8% boost in production: By optimizing equipment usage.
- 15% downtime reduction: By scheduling preventive maintenance tasks.
- 30% reduction in maintenance costs: Thanks to precise planning.
- 70% more productivity: Achieved by eliminating breakdowns.
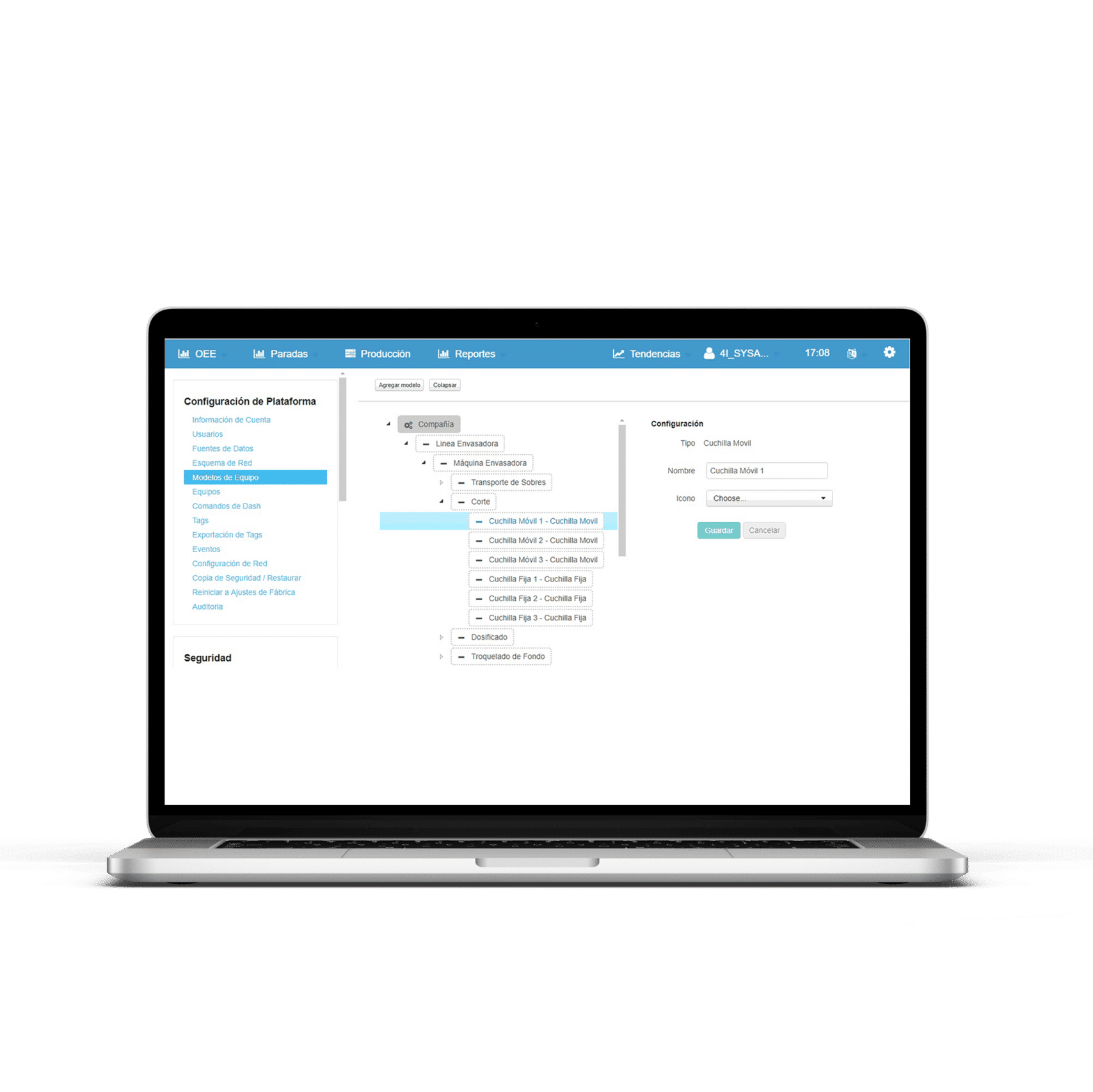
Let’s explore some common manufacturing challenges that ELT addresses:
- Wasted time due to unplanned breakdowns and downtimes: ELT helps you schedule preventative maintenance tasks based on collected data, reducing unplanned downtime, labor, and costs.
- Not knowing a machine’s lifecycle: ELT’s usage trackers provide accurate information about the lifecycle of machines and equipment.
- Not detecting breakdowns in advance: ELT’s real-time data collection allows for the early detection of breakdowns or failures, preventing damage to machines and minimizing productivity loss.
- Higher costs when an asset breaks down during production: ELT enables planned downtimes to prevent breakdowns and associated production losses.
Get in touch with a 4i Platform agent to discover how our solutions can help your manufacturing business run efficiently and achieve better results with OEE formulas.
