We have already discussed the meaning of OEE in other articles, so, hereunder, we will explain how to calculate this productivity indicator and why it is important to do so.
How to calculate OEE?
OEE calculation is used as the main method to assess performance and industrial productivity. Its measurement makes it possible to gather both information and data to analyze if your plant is working at full capacity.
By verifying the effectiveness of your equipment, you will obtain a systemic view of the way in which your manufacturing process functions. In this way, you will be able to rely on strong evidence to make informed decisions regarding improvements, costs reduction, and even possible investments in more efficient machinery.
OEE calculation allows you to line up your production with Industry 4.0’s concept. Thus, your processes will be more efficient, and you will improve and optimize your plant’s productivity. Therefore, you will also add value to your products and services.
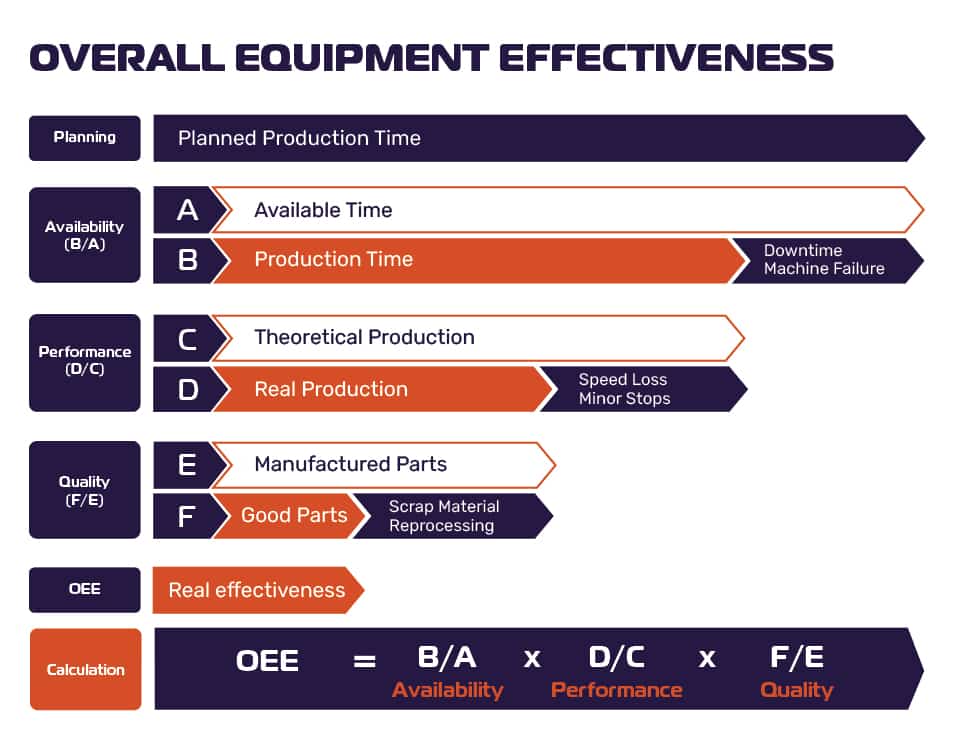
From this calculation, you can learn how much manufacturing time is actually productive. OEE’s calculation is key to reducing losses and improving machine performance. In this way, you will improve machine’s functioning and measure your plant’s productive capacity.
Measuring your equipment’s efficiency will allow you to obtain a complete overview of your manufacturing process, thus gaining information that will help you make informed decisions in terms of improvements, costs reduction and possible investments in more efficient equipment.
The key aspect to bear in mind is that you can only manage and improve what is measured.
Why Measure OEE?
Companies need to improve productive processes by means of identifying inefficiencies which occur during the manufacturing process. It is highly important to recognize the causes of productivity loss and to easily understand the information related to your process.
Besides, identifying and classifying the six great losses of industrial equipment is key to gaining a competitive advantage. The main causes of productivity loss are as follows: equipment failure, setup and adjustments, idling and minor stops, reduced speed, process defects, and reduced yield.
<< Learn about other key concepts: TEEP, OOE, and Takt Time >>
In conclusion, measuring OEE is important, and it has a direct impact both on the company’s productivity and benefits.
With 4i Platform, the integration of data into your manufacturing process has never been easier. Our platform will allow you to improve process efficiency by means of real-time data collection, processing, and analysis. Since data will be in the cloud, both managers and operators will have access to data 24/7 from any device.
4i Platform is customizable, efficient, and easy to integrate into any manufacturing process. If you wish to improve your plant’s productivity, please contact our experts. They will show you how to obtain better OEE scores.
[…] these three parameters which constitute OEE allows you to calculate your OEE score. This calculation will enable you to discover the causes of productivity loss. Therefore, you […]
[…] measures the amount of planned production time that is actually productive. In this article, we let you know how to calculate […]