The management model “lean manufacturing” seeks to minimize losses and it also boosts added value to customers.
Furthermore, this model is based on the idea that waste includes every operation that does not add value to the customer’s experience. For example, operations which involve overproduction, long wait times, and product defects.
Benefits
*Reduce waste
*Improve product quality
*Reduce costs and production time

Five Principles of Lean Manufacturing
These five principles are the basis for lean manufacturing’s implementation. So, to implement these principles, you must:
-define the value your product will add to your clients
-map value stream
-create flow
-establish a pull system
-pursuit perfection
This model can pose several advantages and disadvantages, but these will depend on how lean manufacturing is implemented.
Advantages:
- Time-saving and money-saving model
- Eco-friendly model
- Higher customer satisfaction
- Enhanced safety and well-being of employees
Disadvantages:
- Obstruction of future developments
- Standardization problems
Differences Between Lean and Agile Manufacturing
On the one hand, lean manufacturing aims at near-perfect production. Therefore, it should not be confused with agile manufacturing.
On the other hand, agile manufacturing is a manufacturing methodology that strongly focuses on rapid response to customers, thus considering speed and agility as key competitive edges. For instance, an agile company is in a much better position to take advantage of short windows of opportunity and rapid changes in customer demand.
Relationship Between Lean and Agile Manufacturing
Lean manufacturing is generally considered to be the basis for agile manufacturing. Many lean practices are also enablers for agile manufacturing.
Besides, lean manufacturing tools and techniques can benefit areas beyond the main goal of lean manufacturing (improving productivity and profitability by relentlessly eliminating waste) and agile manufacturing is one of these other areas.
TPM and Lean Manufacturing
TPM (Total Productive Maintenance) uses the lean methodology tools of 5S. Moreover, 5S methodology constitutes the basis for TPM, so it may frequently be a part of a lean implementation.
Furthermore, TPM is a holistic approach to equipment maintenance that seeks for flawless manufacturing:
- No machine breakdowns
- No minor stops or slow running of machines
- No product defects
In addition, TPM values a safe working environment with no work-related accidents.
TPM stresses the need for proactive and preventative maintenance to maximize machines’ operational efficiency. It also blurs the line between production and maintenance operations by insisting on training operators to help with machine maintenance.
<<Implement preventative maintenance on your plant floor today>>
A TPM program creates a shared responsibility for equipment, thus encouraging plant workers to have greater participation in the manufacturing process.
Besides, this method can be highly efficient in terms of productivity improvement (since it increases machine uptime, reduces cycle times, and eliminates machine failures).
Traditional TPM Pillars
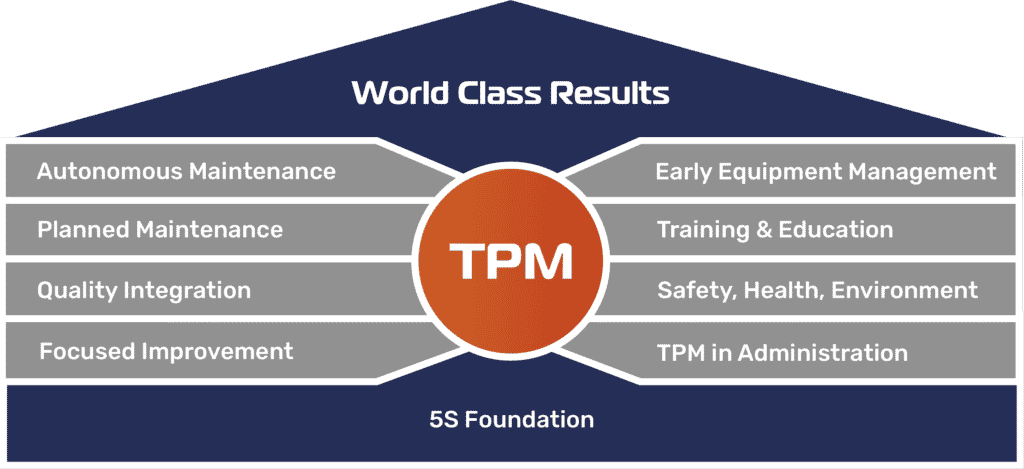
TPM traditional model consists of 5S (sort, straighten, shine, standardize, and sustain) and eight supporting activities.
5S methodology aims at creating a clean and well-organized work environment and it comprises five actions:
- Sort: get rid of any element that is not required in the work area
- Straighten: organize the items left
- Shine: clean and inspect the work area
- Standardize: create standards for the activities above-mentioned
- Sustain: ensure that workers comply with set standards
Turn Lean Manufacturing Into a Reality With 4i Platform
At 4i Platform, we provide you with tools that can help you reduce losses and enhance added value to customers. With our platform, you will also learn what decisions to make to reduce waste and improve efficiency. Learn more about our apps and achieve lean manufacturing in your manufacturing processes.