In the rapidly evolving landscape of Industry 4.0, technological advancements are reshaping the manufacturing sector, ushering in a new era of innovation, efficiency, and skill development. As the industry embraces automation, artificial intelligence, and the Internet of Things (IoT), the demand for a skilled and adaptable workforce has never been more critical.
Embracing Change: Industry 4.0 and Job Evolution
The dawn of Industry 4.0 brings not only new technologies, but also a paradigm shift in the nature of jobs. Traditional roles are changing and new positions are emerging. Manufacturers find themselves at the crossroads of innovation, requiring a workforce equipped with the right skills to navigate this digital revolution.
The Skills Dilemma: A Call for Training and Development
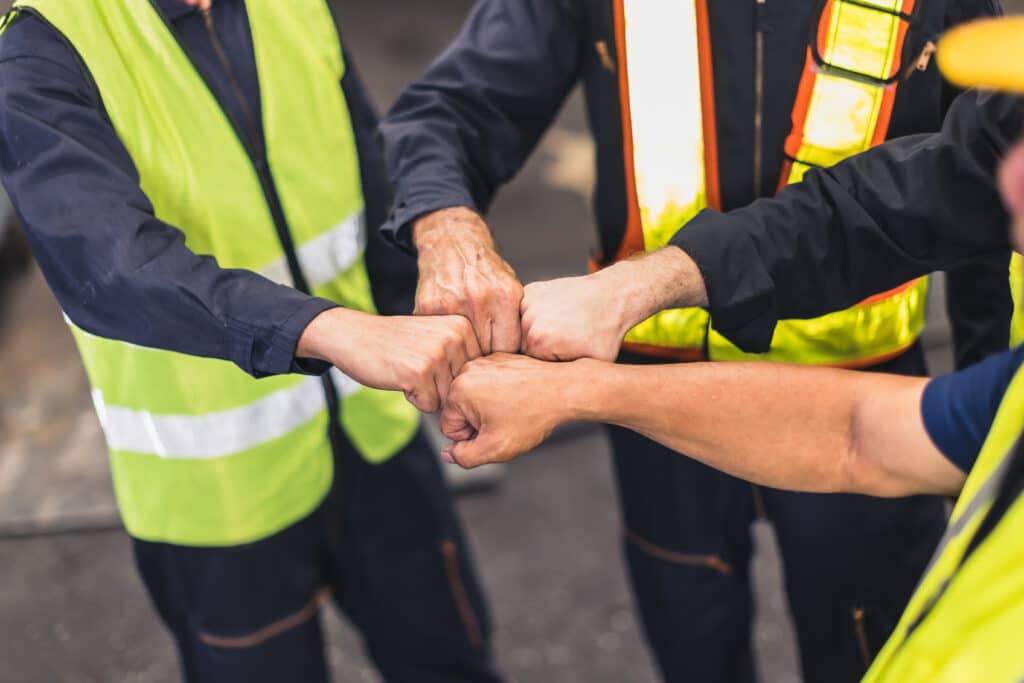
To thrive in the age of Industry 4.0, manufacturers must recognize the imperative of investing in skills development. The skills that were once sufficient are rapidly becoming outdated, making continuous training and upskilling programs essential. This proactive approach is not just a necessity but a strategic move to future-proof the workforce.
What are the new skills required for Industry 4.0?
The new skills required for Industry 4.0 include:
- Technical skills: These skills include the ability to program, operate, and maintain advanced manufacturing equipment.
- Data analysis skills: These skills include the ability to collect, analyze, and interpret data from sensors and machines.
- Problem-solving skills: These skills include the ability to identify problems, develop solutions, and implement those solutions.
- Communication skills: These skills include the ability to communicate effectively with colleagues, customers, and suppliers.
How can manufacturers invest in skills development?
There are a number of ways that manufacturers can invest in skills development for their workforce. These include:
- Providing on-the-job training: This type of training allows employees to learn new skills while they are on the job.
- Offering tuition reimbursement: This type of program helps employees to pay for the cost of training.
- Partnering with educational institutions: Manufacturers can partner with colleges and universities to develop training programs that meet their specific needs.

The benefits of investing in skills development?
Investing in skills development has a number of benefits for manufacturers. These benefits include:
- Increased productivity: Employees with the right skills will be able to work more efficiently and produce more products.
- Improved quality: Employees with the right skills will be able to produce higher-quality products.
- Reduced costs: Employees with the right skills will be able to identify and solve problems more quickly, which will reduce downtime and waste.
- Increased innovation: Employees with the right skills will be able to come up with new ideas and solutions.
Bridging the Skills Gap: The Intersection of Technology and Workforce Development
As Industry 4.0 unfolds, one of the foremost challenges is cultivating a workforce with the skills to thrive in the digital age. This is where 4i Platform aligns seamlessly with the broader narrative of skills development. Manufacturers investing in this innovative platform are not just adopting cutting-edge technology but are actively nurturing a workforce capable of harnessing its full potential.
The Role of 4i Platform in Bridging the Skills Gap
In the midst of Industry 4.0’s transformative wave, navigating the skills development landscape becomes even more crucial. Here, the 4i Platform stands as a beacon, offering a comprehensive digital manufacturing solution designed to propel industrial companies into the future.
4i Platform is more than just a tool; it’s a catalyst for efficiency, productivity, and quality improvement in manufacturing operations. This cloud-based platform seamlessly integrates with various existing systems, such as ERP, SCADA, and MES, making it a versatile and adaptive solution for the modern industrial environment.
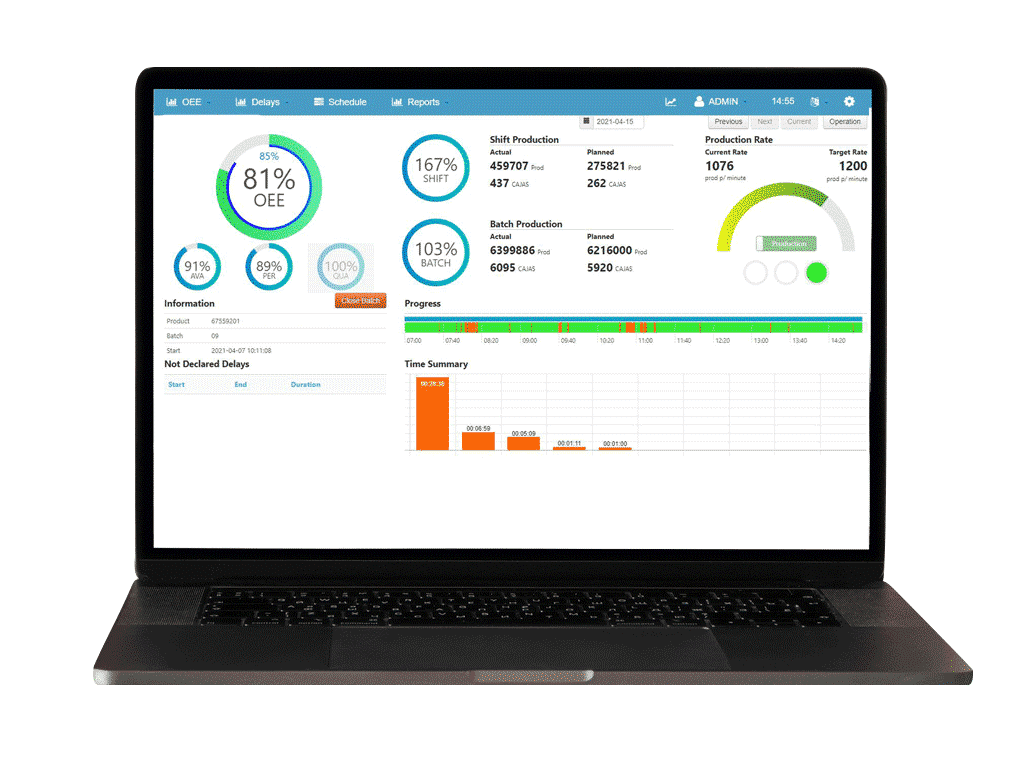
Key Features and Modules:
- Data Acquisition: The platform excels in collecting data from a myriad of sources, including sensors and machines, forming the foundation for insightful analysis.
- Data Processing: Through advanced processing capabilities, 4i Platform cleanses, transforms, and normalizes data, preparing it for in-depth analysis.
- Data Visualization: Clear and concise presentation of data is achieved through intuitive dashboards and charts, enhancing decision-making processes.
- Analytics: The platform goes beyond mere data representation, actively identifying trends and patterns to offer valuable operational insights.
- Machine Learning: Leveraging predictive analytics, 4i Platform forecasts future outcomes and optimizes processes for sustained efficiency.
Industry 4.0 is creating new opportunities for manufacturers, but it is also creating new challenges. One of the biggest challenges is the need to develop a workforce with the skills necessary to succeed in the digital age.
In addition to the benefits listed above, investing in skills development can also help to improve employee morale and retention. When employees feel like their employer is investing in their future, they are more likely to be engaged and productive.
In conclusion, skills development is an essential investment for manufacturers that want to succeed in the Industry 4.0 era. By investing in their workforce, manufacturers can ensure that they have the skills they need to innovate, compete, and grow.